Braskem and Made In Space to send plastics recycler to International Space Station
The goal is to further increase the autonomy and sustainability of space missions while facilitating the day-to-day routine of astronauts, since they will be able to transform plastic waste from items on the International Space Station that have reached the end of their useful lives into feedstock for making new items.
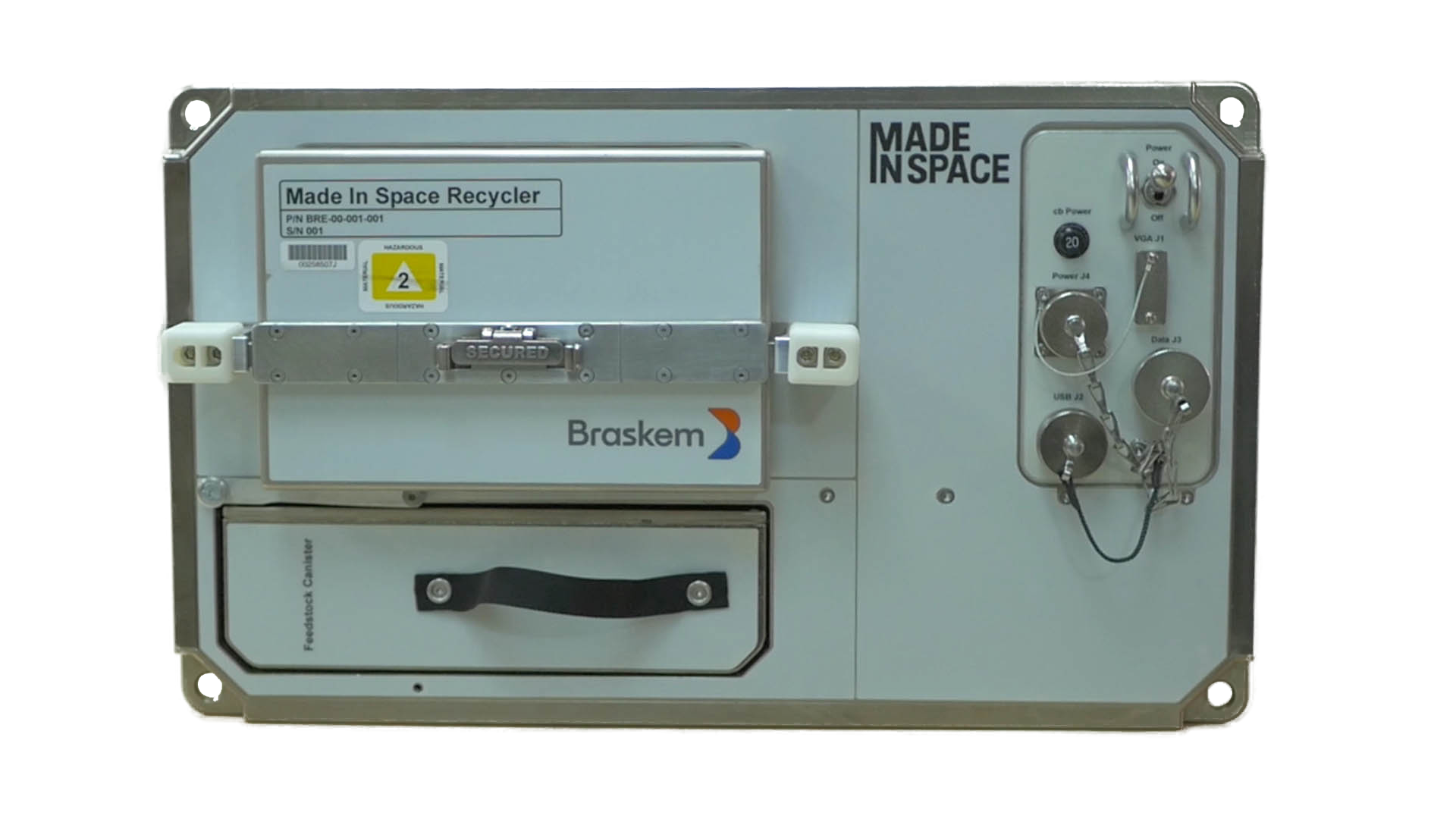
The plastics recycler developed by Made In Space, Inc . a U.S. company contracted by NASA to develop new technologies for operation in zero gravity - in partnership with Braskem - will be launched into space by the 12th commercial resupply mission of Northrop Grumman (NG12) to the International Space Station. The bold project will be the first commercially-developed plastics recycling facility in the history of space missions.
The launch is scheduled for 10:59 a.m. on November 2, Brasília time, from the NASA Wallops Flight Facility, located on Wallops Island in the state of Virginia just off the U.S. East Coast. The recycler should reach the Station 2 days after its launch. The goal is to further increase the autonomy and sustainability of space missions while facilitating the day-to-day routine of astronauts, since they will be able to transform plastic waste from items on the International Space Station that have reached the end of their useful lives into feedstock for making new items.
The partnership between the two companies is one of a series of Braskem initiatives to promote the Circular Economy and is part of Braskem's project Printing the Future , which, in 2016, took to the ISS a 3D printer using Braskem's biobased I'm greenTM PE, made from sugarcane, to fabricate objects in space. "The biobased I'm greenTM plastic was selected due to its combination of properties, such as flexibility, chemical resistance and recyclability. The convenience of on-demand 3D printing of parts and tools increases the reliability and safety of space missions. The space recycler could help, for instance, to replace damaged parts and fabricate tools on-demand. As such, it effectively closes the plastics cycle onboard the Space Station, reducing its dependency on raw materials sent from Earth," explained Fabiana Quiroga, director of Circular Economy at Braskem for Latin America.
The technology used for the recycler to operate in zero gravity was developed by Made In Space and has been in development and undergone extensive testing since 2016. The final flight payload, developed in partnership with Braskem, was assembled and tested in the summer of 2019.
The equipment will break up the plastic waste and unwanted parts, apply heat and produce spools of feedstock from the same polymer. These spools can then be used in the 3D printer to fabricate new objects. The recycling process is automated and requires minimum intervention by the team of astronauts.
The 3D printer, called the Additive Manufacturing Facility (AMF), which has been onboard the ISS since 2016, also was made using Braskem's polymer technology. The printing bed that is used to print objects using I'm greenTM PE is made from Braskem's ultra-high molecular weight polyethylene (UHMWPE), which is marketed under the brand UTEC®. The first part fabricated using the I'm greenTM PE outside of Earth was a pipe connector for a vegetable irrigation system.
"Local manufacturing resources are a crucial capability for space exploration. Demonstrating and validating recycling capabilities on the ISS is an important step towards developing sustainable manufacturing systems that will enable us to venture deeper into the Solar System," said Michael Snyder, chief engineer at Made In Space.
"We believe that innovation helps improve people's lives, whether on Earth or in space. On Earth, we are engaged in joint efforts with our clients, partners in the value chain and society to find more sustainable solutions that use plastics. One of them is the biobased I'm greenTM PE, the world's first polyethylene made from 100% renewable resources, which helps reduce CO2 emissions, a greenhouse gas. And in space, through our support for Made In Space, we have an opportunity to help increase the autonomy of missions and optimize the weight transported. This is a Brazilian technology that is going beyond the boundaries of our planet," said Braskem CEO Fernando Musa.
For two years now, Braskem has been investing in the development of additive manufacturing technologies, also known as 3D printing. The technology enables the fabrication of a physical three-dimensional object based on a digital model by adding successive layers of material. The petrochemical company is expanding the adoption of polyolefins and PVC in this process and developing a portfolio of materials that are ready for printing in the form of extrusion filaments and powders for use in laser syntherization, which will soon be made available to its clients.
About Made In Space
Made In Space, Inc. (MIS) is the world's most experienced space manufacturing company. Established in 2010 and with offices in Florida, California, Alabama and Ohio, MIS leverages the unique properties of the space environment to develop manufacturing solutions to commercial, industrial, research and defense challenges. The company's vision is to enable the future of space exploration by offering off-Earth manufacturing capabilities. For more information about MIS, click
here
.
For more information related to press, please contact:
Fato Relevante
imprensa.braskem@agenciafr.com.br
Related News

Se você é um profissional da imprensa, a Braskem tem um canal feito só pra você.
Acesse aquiPress Releases
More news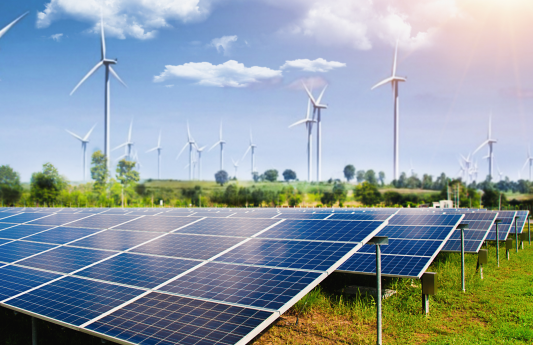
Update on Upsyde
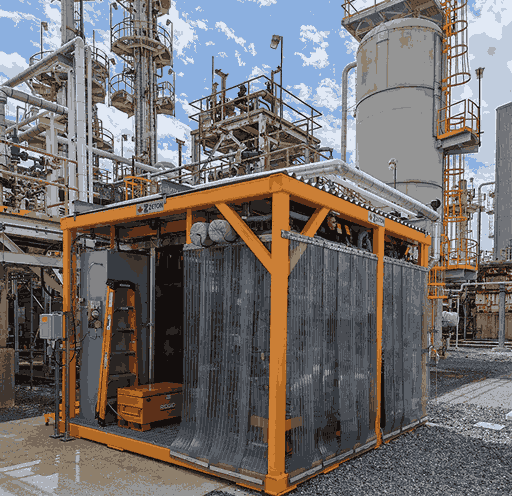
Braskem and Ardent Advance Breakthrough Olefin Separation Technology Towards Commercial Implementation
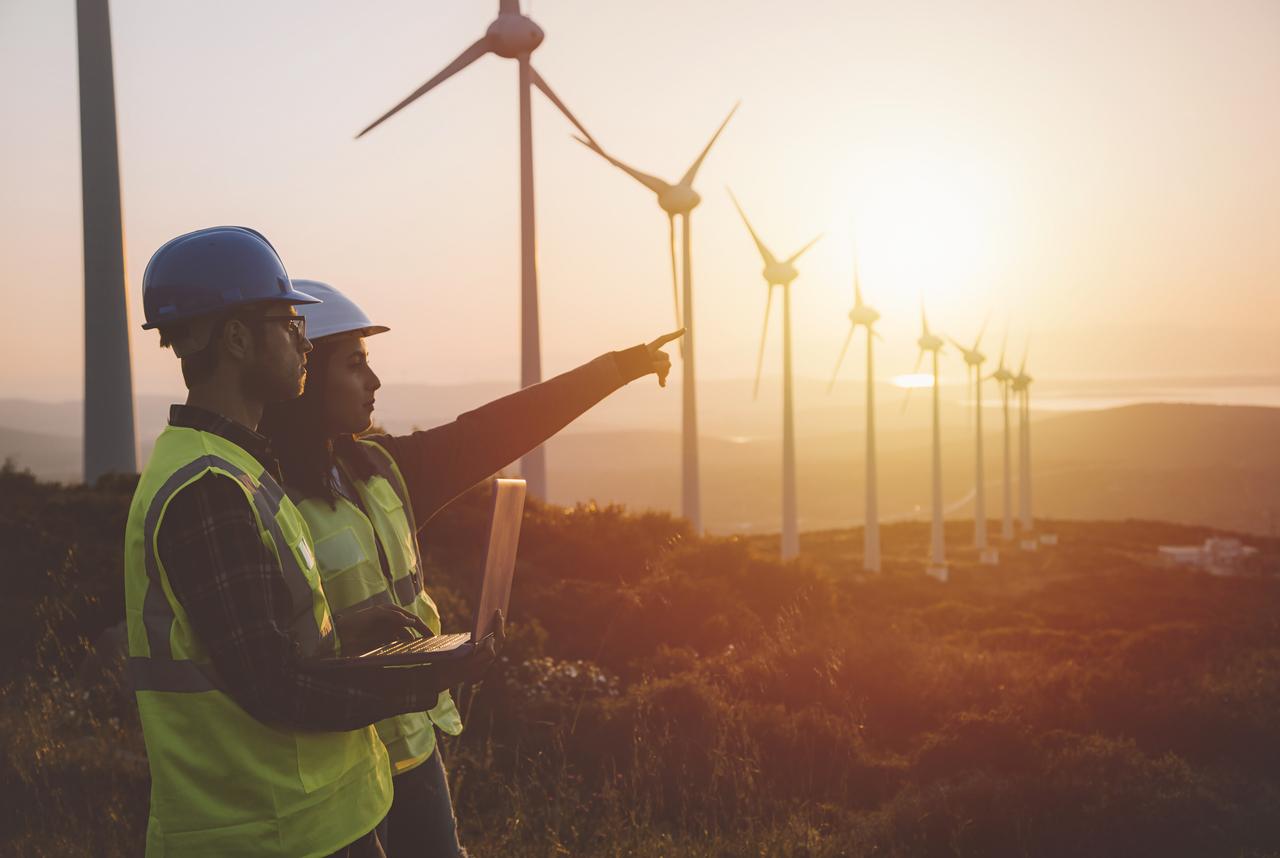
Ranking Highlights Braskem as a Reference in Circular Economy
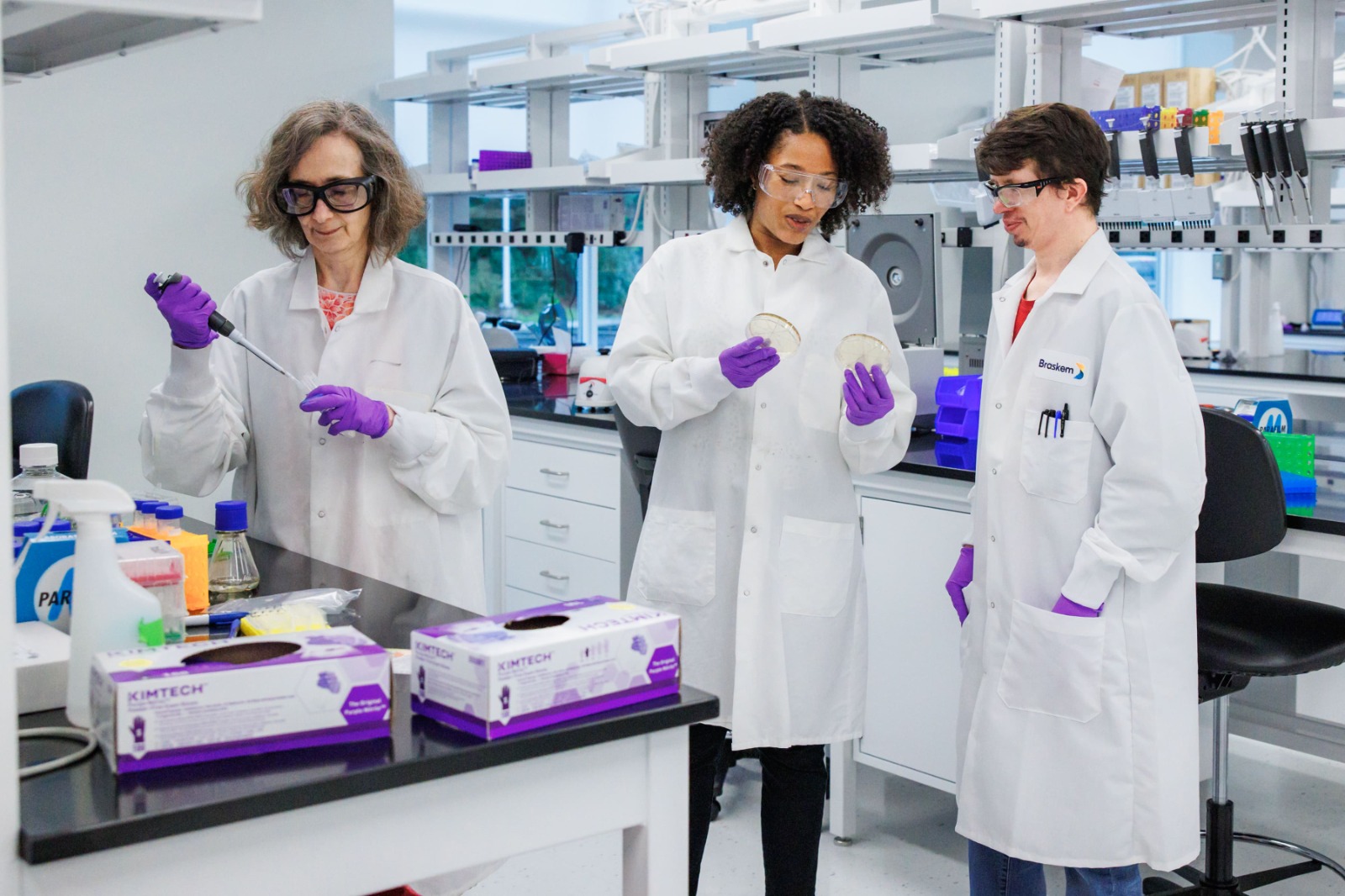
Braskem Announces the Official Opening of its Renewable Innovation Center in Lexington, Massachusetts
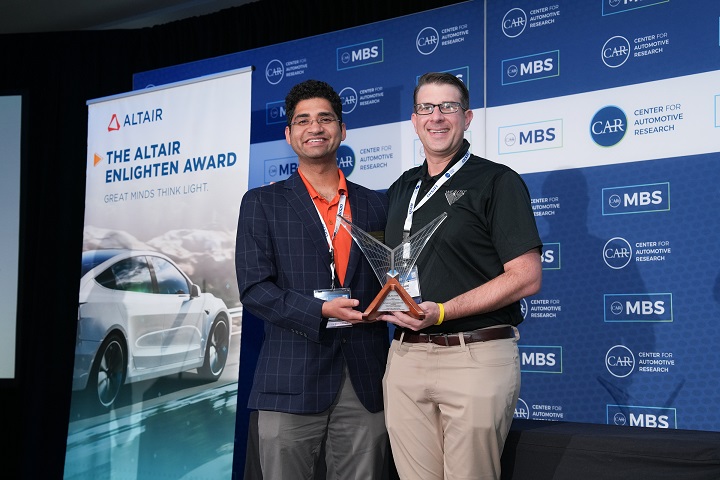
Braskem and WEAV3D® Win the Altair Enlighten 2024 Future of Lightweighting Award
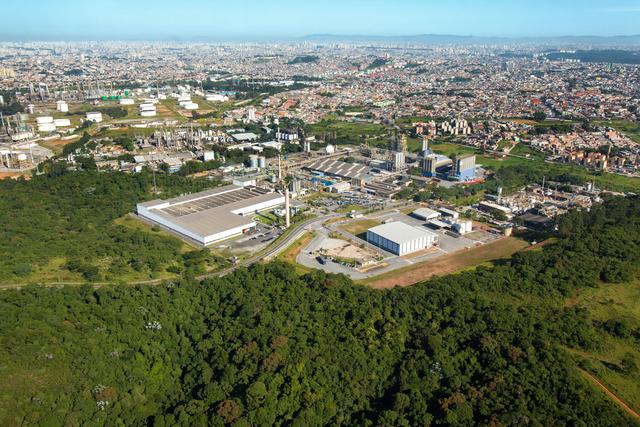
Lummus and Braskem to Partner on Electrified Cracking Heater for Decarbonization
Customers
Become a Braskem customer
Braskem is one of the largest suppliers of chemical and petrochemical products in the world, recognized for its focus on sustainable development, innovation and quality.
We believe in lasting partnerships, we have a broad portfolio of products and we work together with our customers to create new practical and sustainable solutions in all markets.
Talk to our sales team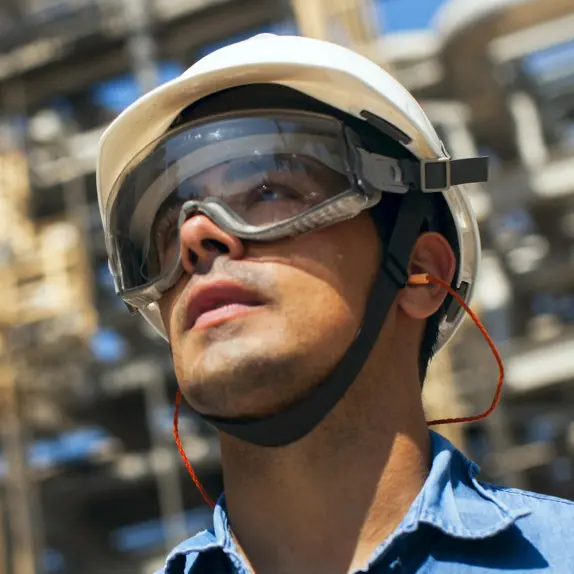
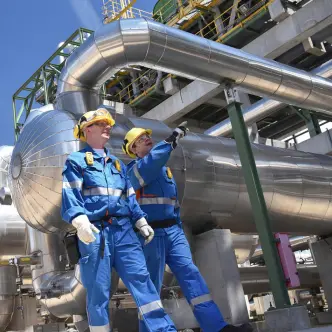